Solenoids Help Control Injection Molding
A manufacturer of foam injection molding machines needed to refine their product to better suit a client that made seats for automotive OEMS. TLX engineers designed a custom latching solenoid that operated in high temperatures and provided the precise control required for the molding process.

Customer Problem
A manufacturer of foam injection molding machines needed to refine their product to better suit a client that made seats for automotive OEMS. The seat manufacturer requested the ability to easily control the density of foam during production so that each seat component could meet OEM specifications. Variations in foam density help ensure good vibration absorption, passenger comfort and long-term durability.
The TLX Solution
TLX engineers designed a custom latching solenoid that operated in high temperatures and provided the precise control required for the molding process. As the injection machine filled the seat mold, a short pulse of power moved the solenoids to the “latched" position. Once latched, the solenoids would open vents in the mold, allowing air and gas to escape as the foam expanded. Permanent magnets held the solenoid open while consuming no power. A short pulse of opposite polarity would de-latch the solenoid once the mold was full; closing the vents and compressing the foam. The latching solenoid operated on four AA batteries and could run efficiently for at least 50,000 cycles.
- Stroke (designed to spec)
- 6.35 mm
- Holding force
- 5.6 N
- Resistance at 20°C
- 2.8 ± .03 Ω
- Spring load (latched position)
- 13.3 ± 1.3 N
- Spring load (de-latched position)
- 4.45 N reference
- Cycle life of 4 AA batteries
- 50,000 cycles min
All TLX components are customized to fit system requirements, meaning technical specifications are unique to each customer and design. Examples given on our website are for illustration purposes only.
Working with TLX
- Experienced partner of industry leaders, first-tier suppliers, and OEMs
- Direct access to our design and engineering team
- Localized production in USA and China
- Dependable single-source solution from design to delivery
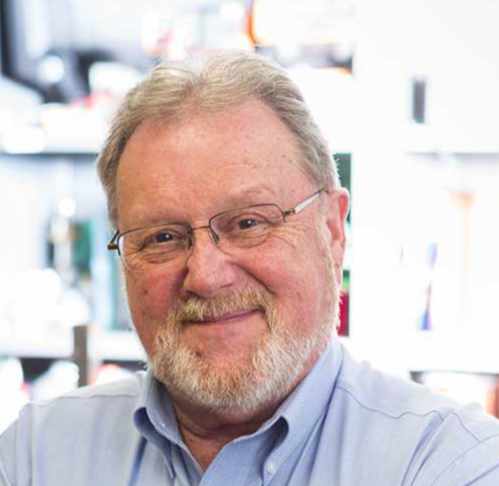
Have questions or ready to get started?
Are you designing the technology of tomorrow?
Start your conversation with a TLX engineer today.