Layering Intelligence into Solenoid Design
Traditional mechanical components, like solenoids, are key parts of a wide range of products, and they can be designed to offer more value than just linear actuation. OEM design teams can support the gradual transition to Internet enabled operations by layering intelligence into their products for improved operations and value to end customers. Including integrated sensing at the component level is a first step toward designing a system that can eventually become Internet enabled.
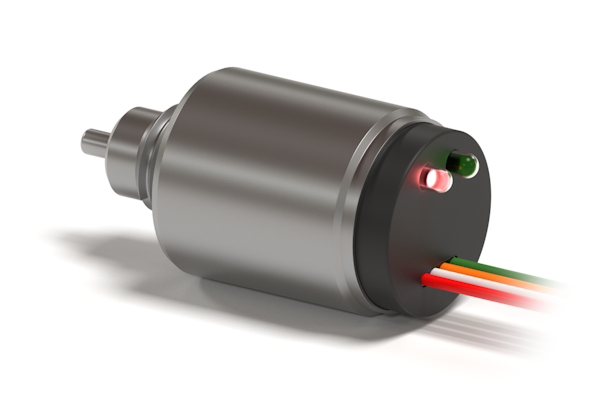
Being able to easily confirm a component is consistently operating within specifications is a key benefit of sensor integration. For example, a latching solenoid can be designed with an integrated Hall effect sensor to detect whether the armature is extended or retracted. The data from the Hall sensor could be sent to a dual color LED. Green could indicate extended, and red could indicate retracted. It is also possible to integrate an internal clock and a tri-color LED. The lighting cues could be the same for green and red with the addition of yellow to indicate that the armature has not moved within a set period.
By adding LEDs to a solenoid, end users will have an easily identifiable visual cue to indicate whether a component is operating properly. This can yield a considerable cost savings both in terms of quality control and maintenance. For example, a carpet weaving machine may have as many as 1,000 solenoids timing its movements. Changes in the lighting pattern on the solenoids would serve as an instant visual alert to a possible quality control issue. This could save, quite literally, tons of material over time because a quality issue can be identified early instead of being detected later in the production process. Maintenance technicians can also easily identify exactly which solenoid is malfunctioning, greatly streamlining the diagnostic and troubleshooting process. For instance, an abnormal lighting pattern at one solenoid may indicate something as simple as a loose electrical connection to the solenoid, which could be quickly and easily remedied.
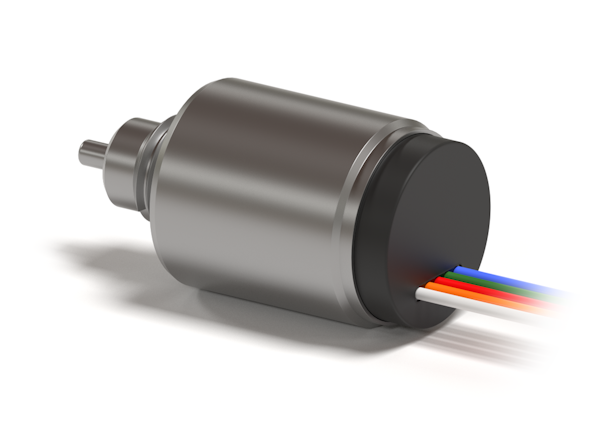
Additionally, the data can also be passed to a programmable logic controller (PLC), which can report on the solenoid’s functions. The data collected by the PLC can be used to determine if it is necessary to stop the production line to perform immediate repairs or if maintenance can be scheduled for a later time when the production line is not running. This can minimize the need to shut down production during peak hours.
The solenoids can also support both LED indicators and information flow to a PLC simultaneously. That gives the OEM design team the most flexibility to determine what works best for the end customer.
By incorporating components with integrated sensing into their products, OEM design teams can provide immediate and tangible value to end customers while laying the foundation for eventual Internet connectivity. This type of innovation strategy allows OEMs the freedom to determine the best timing for adding Internet based communications and related features to their products.
This article was originally published by TLX Technologies in March 2021
Want to explore design examples?
TLX Technologies is the go-to custom solenoid partner of the world’s top brands, first-tier suppliers, and OEMs