Efficient Disconnects
Center Axle Disconnect (CAD) systems are commonly used on part-time four-wheel drive (4WD) internal combustion engine (ICE) vehicles. These systems allow drivers to enjoy the extra traction that 4WD provides, when it is needed, as well as the fuel efficiency of two-wheel drive (2WD) for normal driving. Electric vehicle drivetrain designers are using a similar concept called disconnecting driveline technology to meet some of the unique demands of EVs, which include reducing energy consumption.
The electric motors used in EVs put out a tremendous amount of torque. Using 4WD during vehicle acceleration reduces the stress on the tires and helps the vehicle reach cruising speed quickly and efficiently. Depending on the drivetrain architecture, powering both the front and rear axles can be less energy efficient. On some EV drivetrains, disconnecting the front wheels from the drivetrain during cruising can reduce energy consumption and help maximize range.
On a part-time 4WD ICE vehicle, the CAD uses a shift fork that moves a collar to either engage or disengage the front outer axle shaft from the front inner axle shaft, allowing either 2WD or 4WD operation. Some of these systems, especially on older vehicles, are vacuum operated, but many late-model vehicles have systems that use an actuator driven by a small electric motor and gears.

By contrast, the axle disconnect on an EV disconnecting driveline is often inside the front differential and is actuated by a solenoid. Drivetrains equipped in this way may use a single electric motor on the rear axle and a driveshaft to connect the electric motor to the front axle through a transfer case. To achieve 4WD operation, the coil will pull in and latch against the engaging gear.
Some of these systems use continuous-duty solenoids. These solenoids must draw power to remain in position, buy as the goal of this driveline technology is energy efficiency, continuous-duty solenoids may not be the ideal solution. Latching solenoids may be the best option.
Latching solenoids offer significant advantages over their continuous-duty counterparts. Continuous-duty solenoids are subject to self-heating and require a larger coil to keep them cool and generate the necessary force. They will also draw constant power for as long as 4WD is engaged.
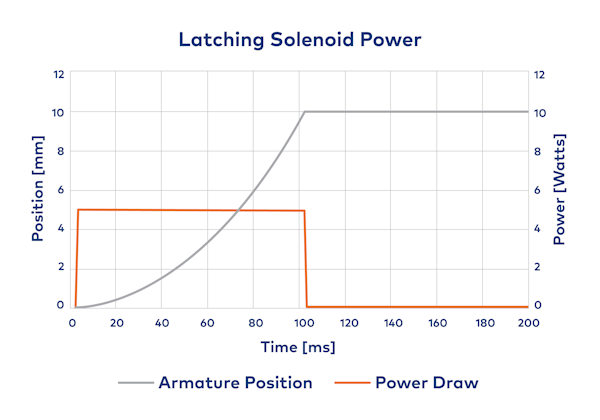
In this application, latching solenoids have many advantages. They use a smaller coil than continuous-duty solenoids for the amount of force they provide, and they are not prone to self-heating. Furthermore, they do not need constant power to maintain a commanded position and require only a short power pulse to change state, usually somewhere around 100ms.
A power pulse of one polarity latches the armature, which is held in position either by a permanent magnet or residual magnetism. A pulse of the opposite polarity releases the armature. Using a latching solenoid in the axle disconnect means that 4WD can be engaged or disengaged with minimal power consumption.
In the quest to maximize energy efficiency, EV drivetrain designers need to utilize the most energy-efficient components available. It could be argued that the power draw of a continuous-duty solenoid is not particularly significant, but when taking into consideration all the other components that are drawing power, any opportunity to reduce power consumption is most welcome. When it comes to axle disconnects for EVs, latching solenoids hold a clear advantage.
This article was originally published by Automotive Powertrain Technology International in June 2023
Want to explore design examples?
TLX Technologies is the go-to custom solenoid partner of the world’s top brands, first-tier suppliers, and OEMs