Coolant Control
In the 1970s, countries across the globe began a decades-long process of implementing mandates intended to improve air quality. Reducing emissions from power plants, industrial facilities, vehicles, and heavy equipment have played a crucial role. This includes reducing nitric oxide and nitrogen dioxide (NOx) emissions, a key contributor to smog and linked to cardiovascular and respiratory disease.
Reducing NOx
Increasing pressure to meet targets for reducing NOx emissions drove manufacturers of diesel vehicles to adopt selective catalyst reduction (SCR) systems. First developed in the 1950s, SCR technology proved effective at reducing NOx and saw its first application in power plants. Now these systems are the standard means of reducing NOx in diesel vehicles.
SCR systems can reduce NOx by as much as 90%. In diesel engine applications, urea, also known as diesel exhaust fluid (DEF), is sprayed into the exhaust stream where it breaks down into ammonia. The ammonia and NOx then flow into a catalyst composed of base metals where they chemically react, reducing NOx to nitrogen and water vapor.
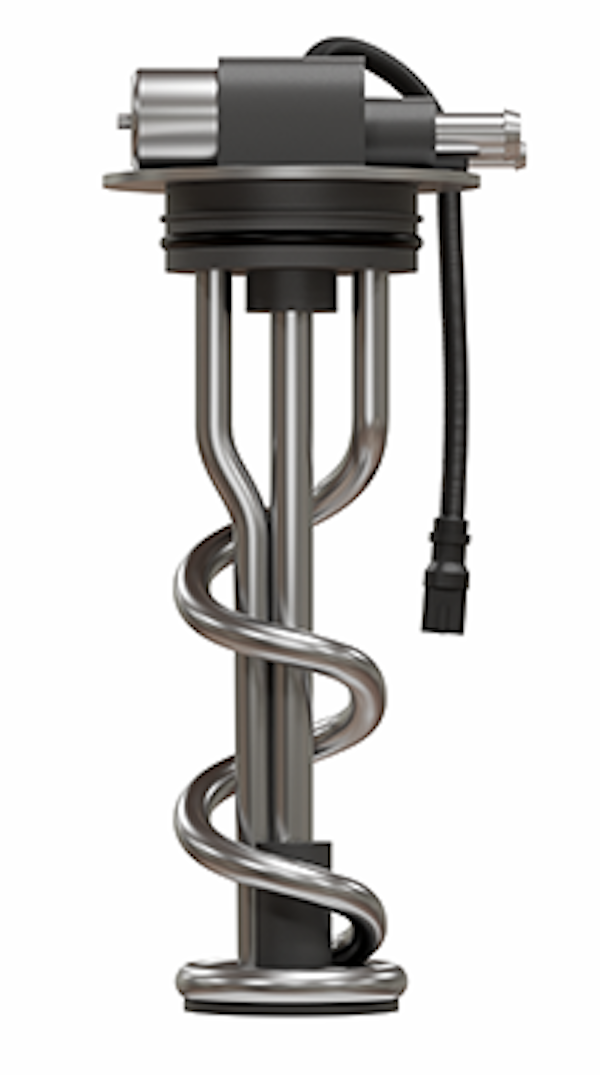
Thermal Management Matters
DEF freezes at temperatures below -11˚C and degrades if it gets hotter than 30˚C. Depending on the specific vehicle, SCR systems may use different thermal management systems for heating and cooling DEF to keep it within its optimal temperature range, between 12˚C and 30˚C.
For certain applications, engine coolant is used for both heating and cooling DEF. Depending on the conditions, hot or cool coolant is circulated through a heat exchanger inside the DEF tank, providing enough heat to keep DEF from freezing, thawing it if it has already frozen, or cooling it if the temperature is in danger of getting too high.
Operating in Harsh Conditions
TLX Technologies was approached to design a coolant control valve for an SCR thermal management system for off-road logging vehicles. The valve needed a maximum flow rate of 0.5 L/s, to be able to handle operating pressures up to 500 kPa, and had to be reliable in harsh conditions that included vibration, submersion, and debris.
TLX developed two versions of this valve: one with an IP65 rating, making it dust-tight and water resistant, and a second with an IP67 rating, making it dust-tight and fully submersible to one meter for 30 minutes. The higher-rated version was needed for vehicles that might operate in circumstances where the valve could be submerged in water, such as during flooding conditions or when crossing a stream.
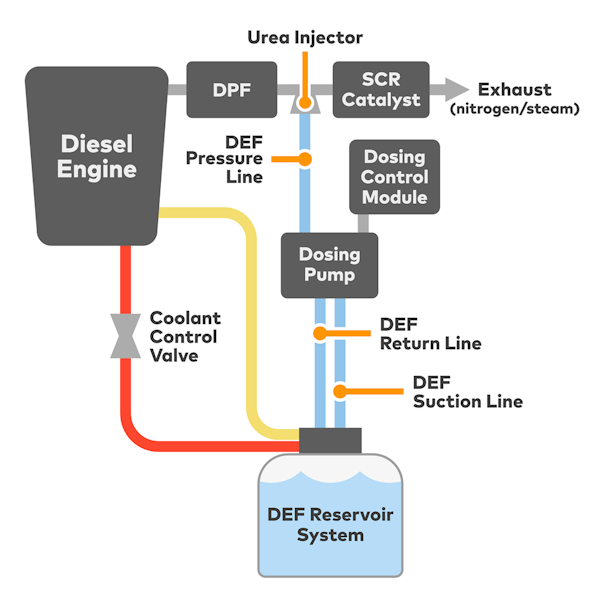
Managing Fluid Contamination
Because logging vehicles are subject to so much dirt and debris, fluid contamination is always a challenge. TLX designed this valve with a custom diverter to route debris in the coolant away from critical internal valve components, ensuring reliable operation even in the worst conditions.
Increasing regulatory pressures are sometimes the driving force of innovation. The added complexity introduced to diesel vehicles by emission control systems requires engineering ingenuity to ensure optimal performance and reliability. As environmental standards continue to evolve, robust engineering becomes not just a compliance requirement but a competitive advantage.
This article was originally published by International Mining Engineer in May 2025
Want to explore design examples?
TLX Technologies is the go-to custom solenoid partner of the world’s top brands, first-tier suppliers, and OEMs